Taking Control of Tooling: Reducing Foreign Object Debris Damage in Aerospace
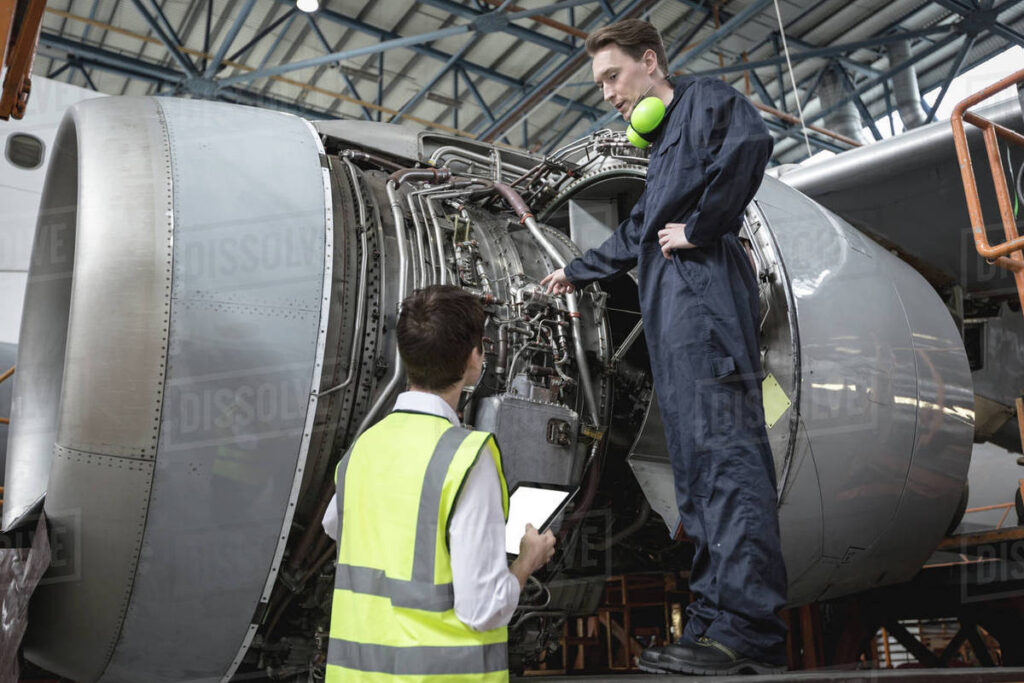
Aerospace organizations worldwide are beginning to implement comprehensive tool control practices to effectively mitigate the risk of Foreign Object Debris damage. Aerospace companies are investing in this FOD management method to prevent equipment damage, production delays, and compromised civilian safety.
The Consequences of FOD
In the safety-critical realm of aerospace manufacturing, tool control and the prevention of Foreign Object Debris incidents are of paramount importance. The devastating crash of a Concorde passenger jet in July of 2000 serves as a haunting reminder of the severe consequences that FOD can inflict. The incident occurred when the aircraft ran over a piece of titanium debris thinner than a centimeter on the runway, causing a catastrophic chain of events in which the tire exploded and flew upwards through the wing and ruptured a fuel tank. Less than 2 minutes later the plane crashed and the lives of all 109 passengers were lost. FOD, including tools and components, poses a safety risk for aircraft passengers and a costly threat to airlines and aerospace companies, with the aerospace industry estimated to lose billions of dollars annually due to FOD-related damages. Aerospace organizations must prioritize tool control to protect the integrity of their engines, aircraft, and reputation. By implementing and maintaining rigorous tool control practices, utilizing advanced storage management solutions, and deploying foolproof tool management systems, companies can mitigate FOD risks and optimize operational efficiency.
The Importance of Tool Control
Tool control is of utmost importance in aerospace manufacturing and maintenance processes. By implementing appropriate tool control systems such as shadowboards, point of use carts, and assembly carts, organizations can effectively track tools and parts, improve efficiency, and ensure quality. These storage management solutions allow line personnel to manage the extensive equipment required for their tasks more effectively.
Custom storage solutions are particularly valuable, enabling teams to easily place tools back in their designated locations. These systems ensure accountability for every tool or part used, promoting organization, and preventing items from being left behind.
Foolproof Systems for FOD Mitigation
To ensure proper FOD mitigation, it is essential for teams to identify every tool used in manufacturing and maintenance processes. Foolproof tool control systems play a crucial role in this effort. Implementing visual tool management systems enables quick and accurate visual inspections to determine if every tool and part is in its proper place.
Shadowboards with 3D cutouts in the exact size and specifications of tools, parts, or components necessary for specific jobs provide clear visual organization and safe handling. Point of use carts can be customized to fit specific needs, while assembly carts ensure the right products are available for each process, minimizing errors, improving quality control, and allowing for safe and easy transport of heavy-duty tools.
Best Practices for Effective Tool Control
As organizations strive to improve tool control and prevent FOD incidents, certain best practices should be followed:
Firstly, it is crucial to implement and maintain tool control protocols to prevent tools and parts from being left in or around the shop floor and production lines. This helps ensure that all tools are properly accounted for and reduces the risk of FOD accidents.
Creating a formal process for tool control is also essential. This process should adhere to manufacturing principles and strict FOD control policies. By establishing a structured approach, organizations can ensure consistency and efficiency in tool control practices.
To reinforce the importance of tool control, employees should be provided with comprehensive training. This training should emphasize the risks associated with misplaced tools and the critical role that tool control plays in FOD prevention. By ensuring that employees understand the significance of tool control, organizations can foster a culture of responsibility and accountability. See fodcontrol.com for more about employee training.
By utilizing smart tool control solutions, the standard methods can be technologically improved. These solutions can include technologies such as RFID tracking, automated inventory management systems, and digital tool check-in/check-out systems. Implementing such systems streamlines tool control processes and reduces the chances of human error.
As manufacturing requirements evolve, it is important to adapt tool storage needs accordingly. This includes accommodating new product line expansions and changing manufacturing needs. By regularly reviewing and modifying tool storage arrangements, organizations can ensure that tool control practices remain efficient and effective.
To foster continuous improvement, open communication should be encouraged by employees. They should feel empowered to provide feedback on additional or improved tool control equipment that aids their work. Employee input can greatly contribute to the refinement and effectiveness of tool control processes. It is often the direct users of the tools who are the most familiar with them.
Original Article: Aerospace Manufacturing