The Remarkable Journey of a Qantas A380 with an Unexpected Passenger
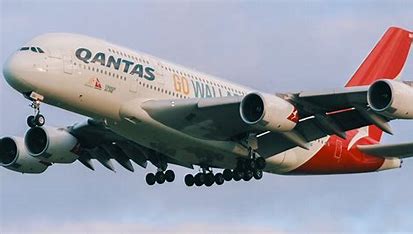
In an unexpected turn of events, a routine inspection uncovered a tool lodged inside the engine of a Qantas Airbus A380. The unusual discovery made in Los Angeles revealed that the tool had been inside the engine for a staggering 294 hours, covering 34 flight cycles, including several transpacific flights to and from Los Angeles.
Investigative Findings
The origin of this unusual situation was traced back to December 6 of last year by the Australian Transport Safety Bureau. The investigation revealed that the tool had been left behind during a maintenance session, remaining undetected and traveling extensively as a result.
This incident highlights the critical nature of aircraft maintenance and the potential consequences of oversight. It serves as a reminder of the importance of thorough inspections and the inherent human potential for error within complex operational processes.
Potential Consequences and Safety Implications
While the scenario might seem like an innocent mistake, the implications it carries are serious and potentially dangerous. The presence of a foreign object within the sensitive mechanics of an aircraft engine poses significant safety risks, not only potentially jeopardizing the aircraft’s functionality but also undermining public confidence in aviation safety protocols.
Fortunately, this story concluded without incident, with the tool being securely retrieved and removed. Nonetheless, the situation invites a review of current maintenance and inspection protocols to enhance the frequency and precision of checks.
This event, though isolated, acts as a prompt for ongoing vigilance in the aviation industry, highlighting the necessity of maintaining the highest standards of safety to ensure the wellbeing of all people who rely on the safety of air travel.
Original article: SCMP